篇首语:本文由编程笔记#小编为大家整理,主要介绍了大数据分析优化技术在催化裂化装置中的应用!相关的知识,希望对你有一定的参考价值。
摘要:催化裂化装置是炼厂生产汽柴油的核心生产装置,是炼厂效益的重要来源。由于工艺复杂,原料重质化,催化裂化装置大多受报警频繁、结焦多等因素的干扰,影响长周期运行水平。随着信息化及智能工厂的建设,工业大数据基础逐渐奠定。九江石化尝试运用大数据分析优化技术,以中国石化炼油技术分析及远程诊断系统及九江石化中央数据库积累的海量数据为基础,进行数据分析、算法研究、可视化应用,对催化裂化装置报警、结焦、产品收率等问题进行探索研究。
关键词:大数据 催化裂化 预警 结焦量化 汽油收率 分析 优化
引言
随着互联网、物联网和云计算技术的迅猛发展,数据充斥着整个世界并逐渐成为一种新的自然资源,大数据技术的研究发展受到了世界范围的广泛关注,其发展势不可挡,且对于提升企业综合竞争力和政府的管制能力具有深远影响。
将大数据技术应用于石油化工领域,国外已进行试验性探索,如BP公司对海量管道传感数据进行分析,发现管道压力数据与管道腐蚀程度的关联关系,可作为管道腐蚀程度的表征,从而更好地安排原油输运,降低腐蚀风险。但国内石化行业对于大数据技术的应用却鲜有所闻。
催化裂化装置加工工艺复杂,是炼油厂生产汽柴油的核心装置,也是经济效益的主要来源。近年来,九江石化两套催化装置经过持续优化,产品分布不断改善,汽油收率大幅上升,在中国石化集团公司同类装置竞赛中排名不断上升,2013年两套催化双双进入前十,2014年1#催化排名第一。两套催化在为企业创造大量经济效益的同时,如何实现“安稳长满优”运行特别是防止沉降器结焦一直是项难题。使用传统工艺技术分析手段进行分析研究,获得了一定的成果,但无法定量地对结焦等问题发生的原因进行跟踪,更谈不上预警与预防,只能被动的事后分析。
2008年3月,中国石化开始炼油工艺远程诊断平台建设,截止至2015年中国石化315 套炼油主生产装置全部实现上线运行,系统三分钟采集一次的数据点数达到16万个,目前存储历史数据约91 TB,且每年以18 TB左右的速度增长,为催化裂化装置大数据平台的建设提供了数据基础。九江石化智能工厂的中央数据库建设将散落在企业各信息系统中的数据按业务主题梳理,并按照智能工厂模型进行集成,可按需提供工业数据作为大数据研究的基础。
基于积累的大量数据和丰富的实践经验,再加上信息科技的日新月异,有条件使研究者与时俱进,采用大数据技术直接利用工业数据建立模型来指导过程的优化,实现装置安全长周期生产及经济效益的提高。本文利用大数据分析优化技术为解决工业问题提供了新思路和新方法。
在中国石化科技部及信息化管理部的大力支持下,作为国家工信部智能制造试点示范企业的九江石化先试先行,率先以“减少可避免的装置报警、预测装置结焦趋势、提高汽油产品收率”为目标开展了大数据技术在催化裂化装置中的应用研究,并进行了工业验证,收效甚佳。研究成果集成到了九江石化数字化炼厂平台,主要功能界面(预警、结焦状况评估、收率寻优)参见图1-1、图1-2、图1-3。

图1-1 九江石化数字化炼厂平台中关键位点预警界面
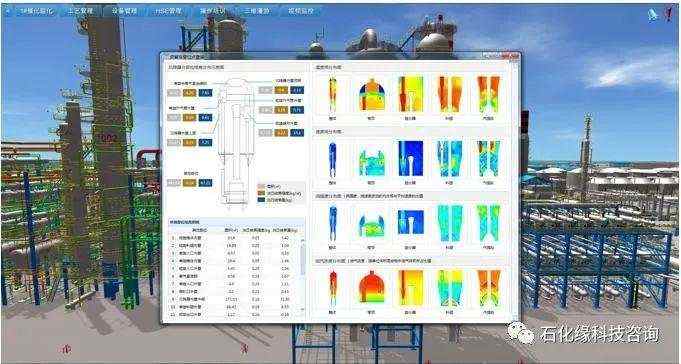
图1-2 九江石化数字化炼厂平台中结焦状况评估界面
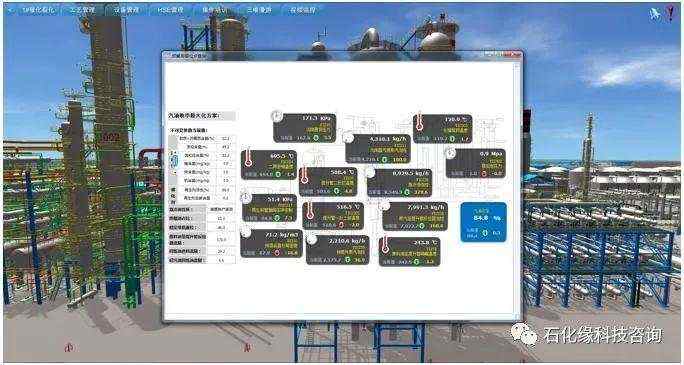
图1-3 九江石化数字化炼厂平台中收率寻优界面
一、催化裂化大数据分析优化技术概述
针对报警问题,本文采用报警管理方法、报警根原因判断技术及预警技术,为企业提供针对不合理报警的判断依据及整改措施,对重要报警提供根原因分析及消除报警的操作建议,并从源头监控,对某些异常工况和关键位点异常波动进行提前判断和预警。
针对结焦问题,本文采用结焦量化技术及预测技术,为企业提供沉降器内部流场分布情况,帮助技术人员掌握沉降器内各部位结焦强度、累计结焦量及装置总体结焦量。
针对收率问题,本文采用参数约减技术、优化技术及降维技术,为企业推送汽油收率的优化方案及操作窗口,帮助技术人员掌握汽油收率的操作空间及优化空间。
在多项技术应用上,本文进行了开创性的研究探索。表1总结了各业务模块所应用的方法、技术及具体采用的算法。
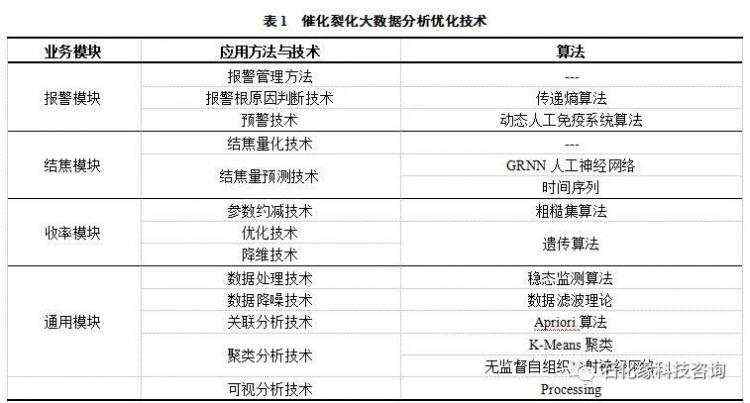
下面针对几项关键技术分别展开介绍。
1、报警根原因判断技术
化工变量之间的根原因分析可以分为基于经验知识、基于模型和基于数据的三类方法。最早的根原因分析是基于经验知识进行分析,但会受到个人经验知识的局限。由于化工过程比较复杂,很难以单一的理论模型进行因果判断,往往是通过数据对模型进行修正。上世纪90年代,由于DCS装置的普及,化工过程中安置有大量传感器,随着计算机引入到每一个工业过程中,从数以百计的变量中采集到大量的数据。数据驱动的根原因分析的研究与应用逐渐兴起,从这些数据中分析出有用的信息,服务于生产安全控制,提高系统的安全性。2000年,Schreiber提出传递熵的概念,用来描述变量之间的信息传递量,根据信息流向来判断变量之间的因果关系。2007年,Bauer等人提出了利用传递熵构建因果图,从而分析扰动传递方向的方法。他们加入了对时滞的考虑,从而符合工业实际。2013年清华大学的舒逸聃博士对Bauer的传递熵表达式进行改进,更加准确表达了变量之间的直接因果和间接因果关系,在过程控制和故障诊断的标准案例——Tennessee Eastman模型上取得了较好的效果,结果证明比传统的Bayes、RBF、SVM方法具有更高的准确率。本文即采用传递熵算法进行报警原因判断,图2展示了位点PT204的某次报警的原因链路图。
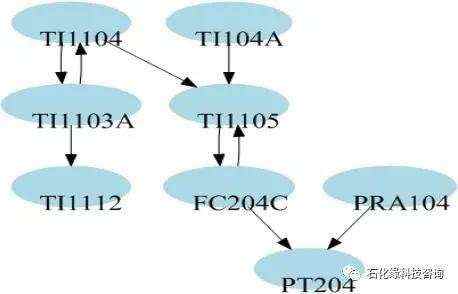
图2 报警原因链路图
2、预警技术
为了保证装置生产的平稳和安全运行,预警模型旨在辅助技术员提前找到可能引发故障的根原因,将其消灭在萌芽中,从而减少报警次数,避免重大的安全事故。关于故障诊断的研究虽然已有四十几年的历史,但由于自学习能力和适应性不足、诊断对象比较理想、鲁棒性差等原因,研究多基于仿真模型,而成功用于实际化工过程的在线故障诊断系统还很少报道。为了解决这些不足,越来越多的研究人员尝试将日益兴起的计算机技术、信号处理、人工智能、大数据技术与故障诊断相结合。清华大学的戴一阳博士将改进的动态人工免疫系统用于化工流程的故障诊断,并利用TE模型验证了算法的可行性。动态人工免疫系统是一种基于过程历史数据的人工智能技术,具有较强的自学习能力和适应性,更新过程相对简单,对数据样本要求较低,符合中国石化催化裂化的工艺特点和数据特点,用于故障诊断并在线预警十分有优势。人工免疫系统故障诊断流程见图3。
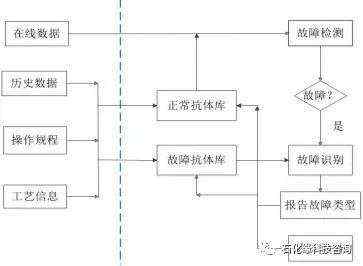
图3 人工免疫系统故障诊断流程图
3、结焦量化及预测技术
在结焦问题上,由于国外催化裂化装置掺渣率较低,且原料多经过加氢处理,沉降器结焦矛盾不大,故对这一问题研究甚少。国内沉降器结焦问题相当普遍而且十分严重,近些年来从工艺、催化剂、工程设计、设备开发及操作管理等方面进行了积极的探索,但是未见将沉降器内各部位焦块进行量化表征的研究报道,而这正是本文的创新之处。本文在沉降器结焦机理的研究基础上,将结焦量化表征,即分解为油浆冷凝率、重油液滴捕获率、重油液滴生焦率,根据九江石化催化裂化装置内沉降器结构构建流场模拟,并对实际焦块样品进行采样分析。基于研究前期采集到的多家炼厂的大量实验数据及流场模拟结果数据,结合催化装置结焦前后实际操作数据形成样本数据,搭建GRNN神经网络及时间序列模型,进行未来时间段内沉降器内结焦量的预测。
4、参数约减技术
催化裂化装置涉及的数据采集位点上千个,大部分位点之间存在或高或低的关联性,冗余度非常高,需筛选出对汽油收率影响显著且相互较为独立的位点进行建模。本项目采用粗糙集算法进行参数约减。粗糙集算法是一种处理不精确与不完全数据的新的数学理论,目前应用颇为广泛,比较适合炼油企业生产数据的处理。它能客观的寻找到数据的本质信息,去除关系小的无用信息,减小数据的信息量,从而减轻人们处理数据的难度,降低工作量,增大处理效率。在本文研究中利用粗糙集算法将参数减少到24 个之后进行收率预测建模。
5、优化技术
本项目采用遗传算法进行汽油收率的优化及降维参数的优化。遗传算法(Genetic Algorithm, GA)是模拟自然界生物进化机制的一种算法,即遵循适者生存,优胜劣汰的法则。它的特点是对参数进行编码运算,不需要任何先验知识,可以沿着多种路径进行平行搜索,不会陷入局部较优,能够找到全局最优点。利用优化技术能够在历史样本库中不断找寻优化操作方案。
6、数据降噪技术
由于化工过程的复杂性,数据有很大的噪声,不进行降噪处理会严重影响系统工作。在Mallat多尺度消噪方法的基础上,Donoho等人提出了一整套基于小波变换的数据滤波理论,被广泛应用于各个领域。该数据滤波理论认为数据噪声为独立同分布的高斯白噪声,并且经过变化之后的白噪声仍然还是白噪声。这种方法的思路,是将原始信号经过小波变换,通过限幅降噪处理之后,然后进行信号的重构,得到降噪之后的数据。以沉降器集气室压力PI210的测量数据为例,图4-1及图4-2展示了降噪处理前后对比效果。
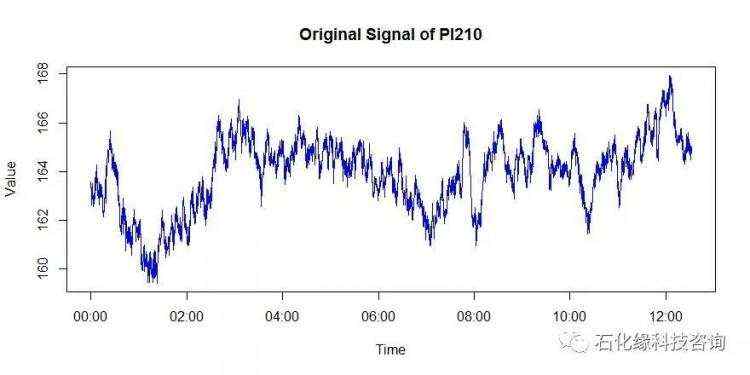
图4-1 PI210降噪前的原始信号
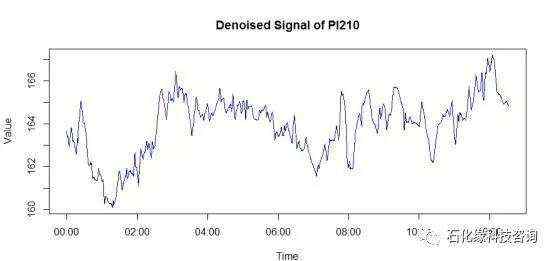
图4-2 PI210经过降噪处理之后的数据
7、可视化技术
近十年来,可视分析(Visual Analytics)逐渐兴起,成为大数据分析的重要方法。大数据可视分析旨在利用计算机自动化分析能力的同时,充分挖掘人对于可视化信息的认知能力优势,将人、机的各自强项进行有机融合,借助人机交互式分析方法和交互技术,辅助人们更为直观和高效地洞悉大数据背后的信息、知识与智慧。面向大数据主流应用的信息可视化技术,包括文本可视化、网络数据可视化、时空数据可视化、多维数据可视化技术等[14]。图5展示了利用Chernoff 脸谱图绘制的催化装置汽油收率与原料性质间的关系图,可直观形象地了解历史操作工况分布。
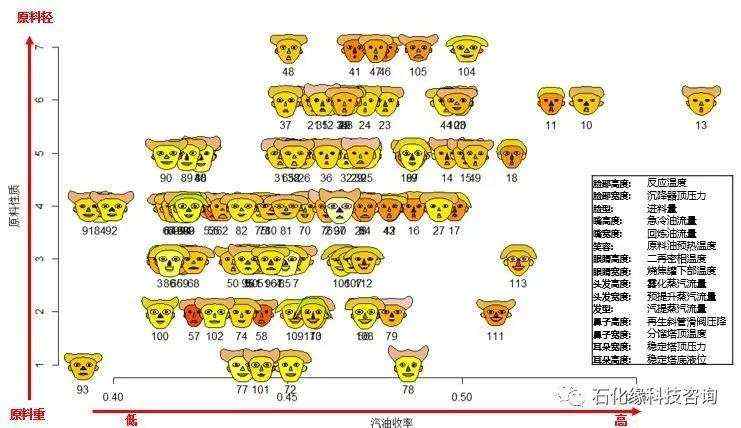
图5 用Chernoff 脸谱图表示的历史操作工况分布
二、催化裂化大数据分析优化技术应用路线
将大数据分析优化技术应用于催化裂化装置,解决实际生产中的报警、结焦、收率等问题,需经历一系列的研究和开发工作,包括:数据采集与整定、算法引擎建立、离线数据分析挖掘、可视分析、各专题技术研究、在线算法开发、可视化开发、在线应用开发、工业验证等诸多环节。下面就主要环节展开介绍。
1、数据采集
基于九江石化中央数据库的实时数据,采集大数据分析所需的原料性质、催化剂性质、工艺操作、报警等数据。利用ETL和CEP的方式进行采集。采集到的数据需要经过以下方法进行处理:野值去除、断点数据去除、疑似数据去除等。
2、建立大数据算法引擎
通过大数据算法引擎,对采集到的数据进行数据存储、数据传输、数据预处理、稳态监测、样本抽取、算法运算、定时调度等任务,是支持功能应用的计算引擎,起到承上启下的作用。技术架构见图6。
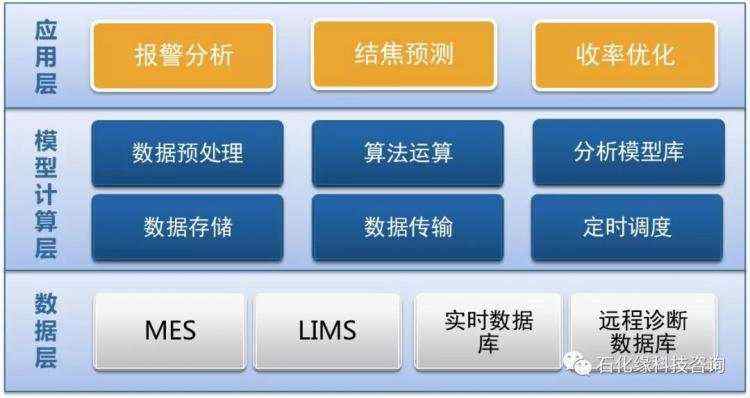
图6 催化装置大数据算法引擎技术架构
3、数据整定
通过数据清洗后,还需要做数据整定。数据整定是根据所定义的具体分析问题,对研究所需的数据进行整定形成样本。整定的依据是企业中央数据库的催化装置、罐区和关联生产设施的多层数据模型。样本库包括基础样本库和专题样本库两个层面。基础样本库开发工作是将采集到的基础数据以时间为统一维度串联各业务主体的数据,形成基础样本库,包括生产物料、质量、计量、操作、工艺等业务主题数据;专题样本库是在基础样本库基础上,利用领域专家的经验选取解决专题问题所需的业务主题数据,形成进行专题分析的专题问题样本库,包括催化报警问题分析样本库、催化结焦问题分析样本库及催化提高汽油(目的产品)收率研究样本库三个部分。
4、技术研究及算法开发
1)报警分析
首先,通过报警管理对报警系统性能进行统计分析,给出报警关键性能指标结果,并通过报警合理化来消除无效报警。接着,结合报警合理化后的报警统计结果、专家和操作人员意见以及生产工艺等因素,筛选出关键报警位点。之后,针对关键报警位点进行基于传递熵的因果链路分析,一方面在故障发生时为操作人员提供指导,另一方面为预警模型的建立提供依据。最后,建立基于动态人工免疫系统的预警模型,对关键报警位点的故障进行提前判断,提高装置的平稳运行。
2)结焦诊断分析
首先,根据结焦机理研究总结,形成油浆冷凝率、重油液滴捕获率、重油液滴生焦率的计算方法。之后,结合多家炼厂原料油实验数据及九江石化结焦前后工业数据,形成油浆冷凝率及重油液滴生焦率样本数据,并根据九江沉降器结构构建流场模拟,总结和观察流场分布(包括温度场分布、压力场分布、速度场分布、油气浓度分布、涡强度分布等),研究重油液滴运动轨迹,根据流场分布数据测算各部位结焦强度,并根据不同边界条件总结形成重油液滴捕获率样本数据。针对停工检修两器打开时的焦块样品,进行采样分析(包括外形、密度、催化剂含量等)。继而,利用总结出的样本数据建立GRNN人工神经网络模型,形成沉降器内各部位及总体结焦量的测算模型,并且利用时间序列算法搭建预测模型,预测未来时间段内结焦量。最后,结合实际应用需求形成结焦恶化原因分析算法并提供结焦量模拟计算模型。
3)汽油收率寻优
首先,基于大数据平台的样本数据(包括各类原料/催化剂性质、操作参数、物料移动等数据),在机理研究和经验总结基础上,利用粗糙集算法结合关联分析得到独立变量24 个,而后利用独立变量搭建神经网络模型进行目的产物(汽油)收率的预测[10],之后利用遗传算法提出优化方案,并寻找逼近最佳收率的最优/最短路径,最后,利用降维技术形成可视化操作窗口图,在最优收率区间内确定操作参数组合,辅助技术人员了解提高收率的途径和关键参数的操作区间。图7展示了一个简易的具有两层隐藏层的神经网络结构图。
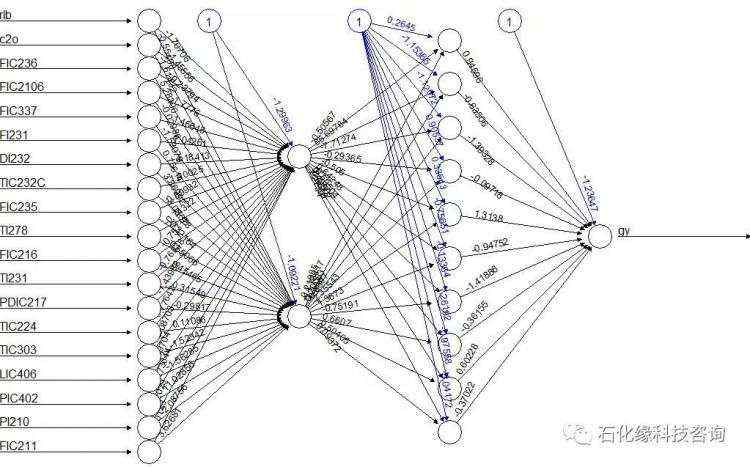
图7 汽油收率测算神经网络结构图
5、应用功能开发
应用功能开发是将研究成果可视化,支持关键用户进行在线的操作。基于样本数据模型进行在线的模型调用分析,利用大数据分析算法引擎进行分析计算,最终将结果进行可视化展示。
6、企业实施及工业验证
九江石化成立了专门的工作组,跟踪项目研发及实施进展,包括技术工作组、项目管理组、信息化支持组。技术工作组负责技术管理及工艺支持,如组织技术讨论、资料收集、工艺对接、提供操作经验知识等工作;项目管理组负责组织协调、推进项目进度;信息化支持组提供实时数据及与其他系统对接等工作。
为了验证研究结果的准确性,在研究过程中九江石化特针对报警原因分析结果、结焦量预测结果、收率寻优结果分别组织了工业验证,及时把握研究方向并对研究算法的准确性给予肯定。比如,完成九江两套催化的结焦量工业验证,预测结果与实际称重较为相符。一套催化装置停工检修时清焦102 吨,大数据预测纯焦量60 吨,以焦块中催化剂占比25%~45%计算,沉降器总焦量为80~110 吨,两相比较偏差小于20%。二套催化装置短停消缺时清焦60吨,大数据预测纯焦量39.8 吨,根据焦块性质分析结果,以焦块中催化剂占比35%~39%计算,沉降器总焦量为61~66 吨,两相比较偏差小于10%。
三、应用效果
本文研究成果已形成完整应用系统,包括报警原因链路展示、关键位点预警、沉降器结焦量预测、汽油收率寻优等功能模块,系统经6个月的在线试运行后,运行效果良好,收到关键用户正面反馈。
预警功能能够做到提前2 分钟(最长提前半小时)成功预警,为技术人员及时采取措施,规避生产风险争取到宝贵时间。例如,2015年12月19日7:27,系统提示对催化装置烧焦罐下部温度低报预警。经观察床温的确在下降。技术员判断是由于原料性质变化导致烧焦效果变差,于是在7:29采取关小外取热滑阀15%(60%à45%)的措施,降低了进料量,之后床温逐渐恢复正常,避免了进一步波动。预警前后对比趋势图见图8。
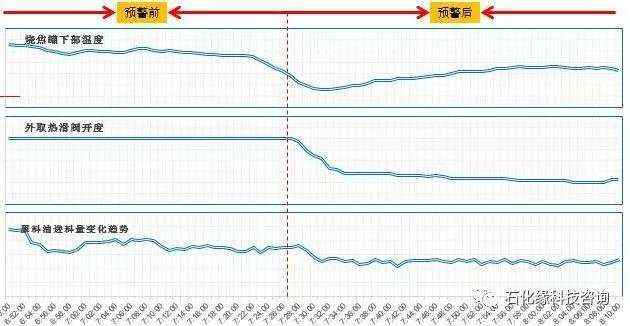
图8 烧焦罐下部温度低报预警
通过综合利用报警合理化手段、报警根原因分析及报警预测,两套催化装置报警数分别降低41.6%及48.8%,提高了装置平稳运行水平。
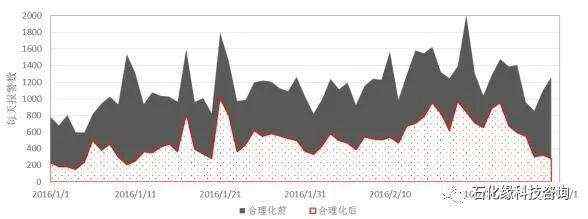
图9 催化装置报警合理化效果统计结果图
结焦量化预测及结焦原因的分析结果帮助技术人员了解沉降器内结焦状况及应对措施,例如,2015年10月27日及30日系统提示沉降器结焦量出现快速增长并给出主要原因,30日技术员查看结焦恶化原因发现:原料残炭含量升高了1%(m/m),沉降器反应油气温度降低了1.83 ℃,而且回炼油流量增加2.42 t/h,同时计算出油浆分压略有增加。随后技术员根据提示结合实际生产需要进行了操作调节:提高反应温度、降低回炼油量,结焦计算量自31日逐步降低。结焦量状况评估及结焦风险趋势图见图10。
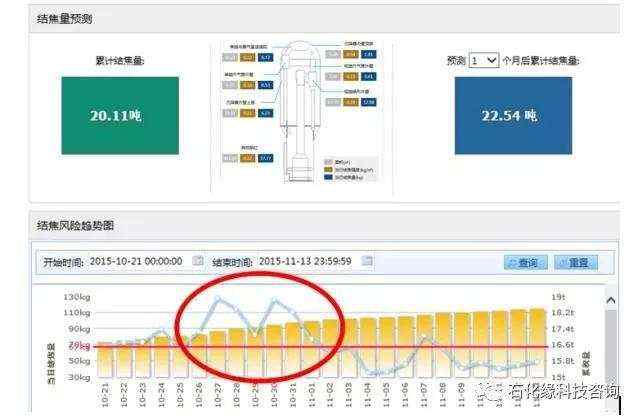
图10 结焦量状况评估及结焦风险趋势图
九江石化两套催化装置在2015年期间保持高负荷前提下实现了正常平稳运行,未发生非计划停工。
汽油收率寻优功能提供优化调整方案,并提供操作窗口,成功助推九江石化两套催化装置的汽油产率稳步上升,变化趋势见图11。据保守估计,大数据技术对汽油收率提升的贡献度可达50 bps。
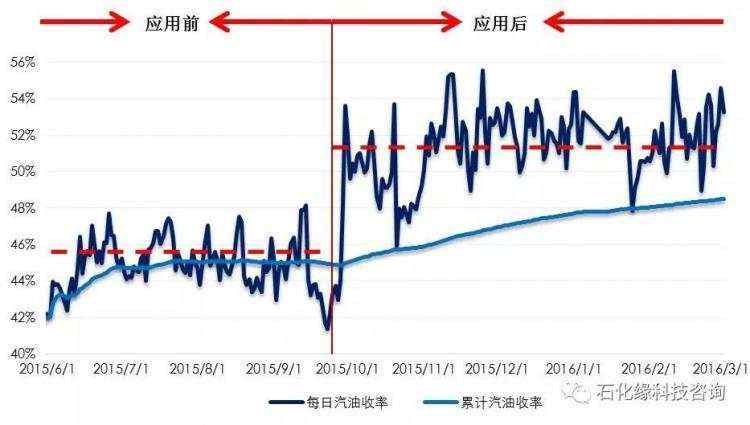
图11 催化装置汽油收率变化趋势图
四、结论
本文探讨了将大数据分析优化技术应用于炼油工业中催化裂化装置的报警、结焦、收率三方面问题。由于催化裂化过程的复杂性,大数据分析优化技术在上述三个问题方面较传统的基于经验和过程知识的解决思路体现出独特的优势。大数据分析优化技术的工业化应用取得了良好的经济效益和社会效益,并将进一步促进大数据技术在石化行业的推广应用。
(转载自 覃伟中 陈齐全等 石化缘科技咨询,版权归原作者所有,如有侵权请联系我们)